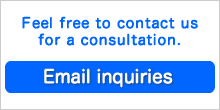 |
Unit washing equipment for washing of heat exchanger pipes |
Automatically washes the inside of the heat transfer pipes while the cooler is running without any loss of performance. |
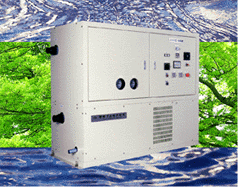 |
Automatic washing of the inside of the heat transfer pipes while the cooler is running without any loss of performance
・ Greatly reduces the power consumption of the cooler
・ Free of periodic manual maintenance
・ Increases the life of the cooler
・ Overall high cost performance |
|
 |
Issues with coolers up until now |
The interior of the cooler condenser heat transfer pipes is dirtied by the cooling water.
This dirt significantly reduces the capacity of the cooler condenser, and not only prevents the cooler from performing to its full potential, but also increases the load on the condenser which leads to wasted power consumption. In cooling tower type coolers in particular, because they are open to the atmosphere, the cooling water gets dirty easier which causes the inside of the pipes to dirty earlier, often exceeding the acceptable ranges, which requires operation stoppages and periodic manual cleaning.
In addition, the effects on the environment of the chemical products used in this cleaning are also a worry. Moreover, in some situations this dirt adhesion also causes electrochemical corrosion which can reduce the life of not just the heat transfer pipes, but the main cooling unit itself. |
 |
Landmark unit washing equipment system |
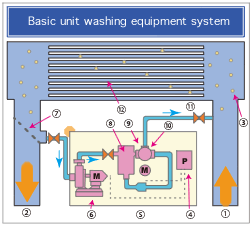 |
Turning the power on drives the "ball circulation pump" and starts circulation of the cooling water from the "ball collector" side to the "ball injection pipe" side. Inside the unit, sponge balls inside the "ball collector" are pushed along by the flow of the cooling water and released inside the "cooling water pipes". The released sponge balls are pushed by the flow of the cooling water and pass through the "heat transfer pipes" while cleaning their interior surfaces. The exterior diameter of the bumpy surfaces of the sponge balls is designed larger than the inner diameter of the heat transfer pipes, so the interior of the pipes and unit are efficiently cleaned during a fixed time circulation. Once the unit operation time that is set beforehand ends, the sponge balls are recovered from the "ball collector", and operation is stopped. |
1. Cooling water inlet , 2. Cooling water outlet , 3. sponge balls , 4. Operation panel
5. Check valve , 6. ball circulation pump , 7. ball collector , 8. ball collector , 9. Ball checker
10. Automatic transfer valve , 11. ball injection pipe , 12. heat transfer pipes
|
|
 |
Unit installation |
This machine is a single unit logically composed of a circulation pump, collector, automatic switching valve and operation panel. The pipe layout also has a simple structure, allowing for installation in any location. |
 |
Easy to operate |
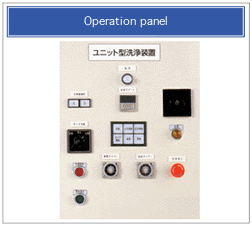 |
All machine operation is controlled by simple switches, so it can be easily operated by anyone. The machine also has an "automatic mode", so it can be simply operated without stopping your company's operations by turning on a single switch. Even in the event a problem occurs, an "alarm buzzer" securely provides notification of the error. |
|
 |
Merits of installing unit washing equipment for washing of heat exchanger pipes |
The unit washing equipment for washing of heat exchanger pipes automatically cleans the inside of compressor heat transfer pipes during cooler operation which eliminates the need for periodic manual cleaning and chemical cleaning, making it more environmentally friendly. In addition, because there is no stoppage of operation for cleaning, this increases operating efficiency and also greatly saves on power consumption compared to before installation. It also prevents causes of electrochemical corrosion etc., so increases not only the life of the heat transfer pipes, but also of the cooler itself, providing both energy and cost savings.
Operation is carried out using easy to understand switches and gauges, so the equipment can be operated by anyone. |
 |
Estimate calculation of annual energy savings when the unit washing equipment is connected to a turbo cooler. |
Estimate calculation conditions |
Item |
Unit |
Specifications |
Cooling capacity |
RT(USRT) |
400 |
Annual operation time |
h/Year |
3,000 |
Annual average load ratio |
% |
75 |
Cooling water inlet temperature |
℃ |
20 |
Cooling water outlet temperature |
℃ |
5 |
Contamination coefficient |
Before installation |
㎡h℃/kcal |
0.0004 |
After installation |
0.00005 |
|
|
|
Energy saving merits |
Item |
Estimate value |
Energy consumption before installation (kW/Year) |
774,900 |
Energy consumption after installation (kW/Year) |
624,900 |
Reduction merits (yen/Year) |
3,000,000 |
Periodic cleaning costs (yen/Year) |
200,000 |
Overall merits (yen/Year) |
3,200,000 |
|
|
|
|
|